wienerberger UK partnered with British Steel, Heatcatcher Limited and Low Carbon Europe Limited in a knowledge exchange project, co-ordinated by The Materials Processing Institute.
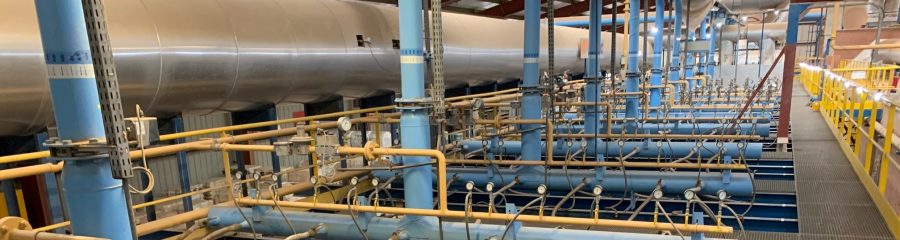
wienerberger UK partnered with British Steel, Heatcatcher Limited and Low Carbon Europe Limited in a knowledge exchange project, co-ordinated by The Materials Processing Institute.
As both steel and ceramics manufacturers use gas-fired furnaces in a continuous production process at temperatures in excess of 1000°C, this project sought investigate approaches to waste heat recovery from furnaces and highlight best practice in energy management, aiming to improve energy efficiency and reduce carbon emissions.
During this project, wienerberger’s Stephane Vissiere (Head of Major Projects & Energy) and Greg Crownshaw (Thermal Process Engineer) visited a British Steel production facility and shared their expertise on how to conduct thermal mass balances for the firing process. The project team then visited two of wienerberger’s brick manufacturing facilities and were able to compare and contrast British Steel’s furnace with wienerberger’s brick kilns. wienerberger’s engineers identified some waste heat recirculation practices that might be applicable to ceramic production. Specifically, this could involve reusing heat from cooling systems to pre-heat the combustion air in brick kilns. Applying this technique to brick kilns could reduce the amount of gas used in the process, and in turn the carbon emissions from wienerberger’s operations.
The project team also exchanged perspectives on how the firing equipment currently in-use could be adapted to successfully introduce hydrogen to the fuel mix. This is important as plans to inject hydrogen into the gas transmission and distribution networks are outlined in the UK Government’s Net Zero Strategy and will help to reduce the carbon content of gas consumed the Foundation Industries including steel and ceramic manufacturers.
This project was part-funded by Innovate UK through the Fast Start Competition, a research and development fund enabling multi-sector industrial R&D projects and feasibility studies addressing shared resource and energy efficiency challenges. The Fast Start Competition is part of the Transforming Foundation Industries Challenge.
wienerberger’s staff have shared these findings withsustainability.html other ceramic manufacturers at the British Ceramic Confederation’s Low Carbon Working Group to encourage the take up of improved technologies and waste heat recovery. Altogether, the results of this project have been shared across Foundation Industry companies operating more than 40 brick kilns and 20 steel reheat furnaces in the UK.
This project demonstrates cross industry collaboration to reduce carbon emissions, evidencing manufacturing process innovations and moving forward together with our partners, two components wienerberger’s sustainability strategy ‘Let’s Build Beyond’.