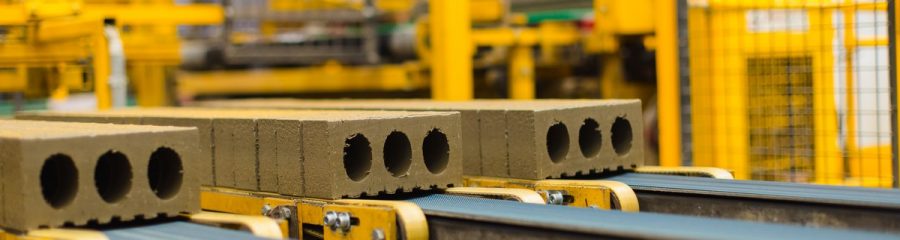.jpg)
The process of making bricks begins with clay, a component of sedimentary rock commonly found on floodplains, riverbanks, or where bodies of water used to be. What makes clay special is that it becomes plastic and mouldable when wet but becomes hard and durable when fired. Clay has been used to create pottery by humans since at least 14,000 BC, with the earliest brick structures dated at 7,000 BC in Turkey.
Clay is excavated from natural clay quarries and stockpiled, levelled with a bulldozer. The clay is stockpiled in layers of different types of clay taken from different parts of the quarry.
To begin the process of manufacturing bricks, the clay must be prepared. The raw material is transported from the stockpile to the production factory, where it undergoes a process of grinding and milling. This breaks down the raw clay, making the particles a more consistent size and shape.
At this stage, water, sand and other additives, such as recycled or secondary-sourced materials, are mixed with the clay. Colour pigments can be added to change the fired colour of the clay brick, while some additives are used to help the firing process or make the finished product even stronger.
The two most common types of brick are named after the way they formed. An extruded brick is produced when clay is passed through a vacuum chamber and through an extrusion dies, which forces the clay into shape. The resulting rectangular column is then wire-cut into individual bricks.
Soft mud bricks, however, are made with a very soft clay, containing a higher proportion of water. These bricks are pressed or thrown into moulds then turned out onto a tray. In the past, this would have been done by hand, but modern soft mud machines can produce tens of thousands of moulded bricks every hour.
Once the bricks have been shaped by extrusion or soft mud moulding, they must be dried before firing. The bricks are stacked and transported to the dryer. This draws out moisture from the soft bricks, also called “green” bricks. The drying period can range from four to 45 hours, depending on the product. The moisture content of the clay drops to below 2% and the brick is ready to be fired.
The dried bricks are transported to large industrial kilns where they are fired at 1000 to 1100 degrees Celsius. This extraordinary temperature is essential to give the clay its durability, strength, and fire resistance – all qualities that make brick a popular building material.
The temperature, the rate at which the temperature increases, and the atmosphere of the kiln all have an impact on the finished brick. These factors are carefully monitored to ensure the consistent quality of each brick.
After the fired products have cooled, they undergo a quality inspection and are packed ready for dispatch. If a fired product does not meet our strict quality tests, it will be separated and recycled. Common recycling routes include crushing for aggregate or recycling back into our manufacturing process.
Once secure in packs or on pallets, the finished product is distributed to builder’s merchants, housing developers and contractors across the UK, ready to be used on-site.
When quarries reach their end of life they can be restored to natural habitats where wildlife can flourish.
Many wienerberger sites have areas listed as nationally important Sites of Special Scientific Interest (SSSI) or local designations for ecological or geological significance. These sites are managed to maintain and promote biodiversity. Management techniques include tree and hedgerow planting, coppicing on rotation and mowing to maintain wildflowers and herbs which in turn support a variety of insects and small mammals.