What is circular economy and how can we apply it
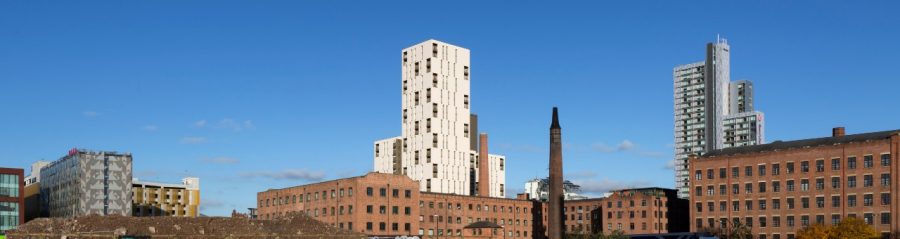
What is circular economy and how can we apply it
I wrote a blog in 2015 outlining challenges and opportunities facing the construction sector as we transition to a circular economy. Much has happened since then, as evidenced by the variety of interpretations presented by manufacturers, contractors, designers and researchers at the Green Construction Board’s conference in January1. Circular economy concepts are being developed and trialled so fast that the Construction Products Association has created a Knowledge Resource for Circular Economy Thinking in Construction just to keep pace with the subject2.
To date, many manufacturers have focused on the potential to reuse and/or recycle their existing products whilst pioneering companies have begun to consider how we would deconstruct buildings and reconstruct them someplace else. These interpretations are by no means incorrect, in fact in some circumstances deconstructing a building and then using refurbished or remanufactured components to rebuild in another location might be the most appropriate option. However, in doing this the industry risks creating a solution for a problem that is not the most important one we need to solve.
This is because the circular economy, as many of us know it, is best applied to products with a short lifespan and high turnover rate (e.g. small electronics). If we design buildings to last 30 years with the intention to replace them several times thereafter we could end up using more resources than if we had designed an adaptable building that will be in continuous service for 100 years or more. The real problem we need to solve is how to design, construct and maintain healthy buildings that will accommodate the changing needs of various occupants over a century, whilst using as few natural resources as possible.
Therefore an interpretation of the circular economy for the built environment needs a different approach to many of the existing models which have been designed for consumer goods. It needs to have the principles of longevity, quality and adaptability at its core, and encourage value chain collaboration so that buildings can morph from commercial to domestic or residential use (and back again) without having to deconstruct or demolish a site. If this approach were to be fully realised it is possible that asset managers could maximise rental income and natural resources could be conserved. The Brick Development Association’s sustainability committee have designed a model depicting ‘four fundamentals of design’ which will facilitate the transition to a circular economy in the built environment (see image below).
These four fundamentals of design offer practical applications of circular economy Principles 2 and 3, as defined by the Ellen McArthur Foundation3.
Design for longevity: the use of durable components in the building fabric (e.g. roof, walls and floors) and applying a ‘systems thinking’ design approach to deliver optimal day-to-day building performance and to provide for long term resilience to climate change.
Design for service: enhancing the experience of the occupant by building for quality, using materials that require low maintenance, are non-toxic and allergen free. The building’s design, layout and furnishings should promote occupant wellbeing and facilitate high productivity.
Design for reuse and refurbishment (at multiple scales): It should be possible to upgrade or repair fixtures and refurbish furnishings in order to minimise consumption of natural resources. The building’s layout should provide adaptable spaces; enabling occupants to change how areas are used (e.g. loft to bedroom). At the macro-scale buildings should be designed with changes of use in mind (e.g. commercial to residential).
Design for material recovery: BIM will enable asset managers to schedule maintenance programmes for fixtures (such as boilers and solar panels), and the ability to identify original manufacturers of components will facilitate repairs and upgrades instead of direct replacement. BIM also provides demolition contractors with an accurate bill of materials so that, if a building must be deconstructed, valuable components can be targeted for recovery and reuse whilst other materials can be marked for recycling. This final design fundamental aims to maximise resource utility if a building must be deconstructed.
This vision of a circular economy establishes the building (domestic, residential or commercial) as the final product and the individual construction materials (i.e. bricks, blocks and roof tiles) as components. This distinction is essential for the realisation of a circular economy, as a holistic approach invites all stakeholders to consider the impact of their role in maximising and sustaining the value of the components (i.e. natural resources) within the building.
Critically, the model also acknowledges that human decision-making has an influence on the circular economy, which many early interpretations have failed to address. If occupants are dissatisfied with their environment they are more likely to make changes to the fixtures and fittings before these components reach the end of their stated service life. Therefore constructing a quality building that promotes occupant wellbeing will be a critical success factor in achieving a circular economy.
We believe that BIM will play a pivotal role in developing a circular economy for the built environment. Not only does it facilitate better design through a digital platform for ‘systems thinking’ (the collaboration of multiple stakeholders); it will lead to more effective long-term asset management and will ultimately decrease the consumption of natural resources in the built environment.
[1] Principle 1: Preserve and enhance natural capital by controlling finite stocks and balancing renewable resource flows is not addressed in detail since this principle can be pioneered by component manufacturers via the component design and manufacturing process. It is anticipated that this is addressed before components become part of the final product: the building.
Explore our sustainability tips and advice pages for guidance on adding environmental and social value to your project.
Discover how we have embedded sustainability into wienerberger's corporate strategy.